The raw materials for polyethylene pipes for water, gas, oil, municipal and industrial wastewater are usually HDPE, PE80 and PE100 materials.
In order to produce polyethylene pipes, the extruder used must be of the best quality so that the product obtains the required quality. The raw materials used must be new and free of any additives other than the masterbatch required in the tube. The correct and controlled production method prevents oxidation of polyethylene materials and non-burning materials, which increases the quality properties of polyethylene pipes, including resistance and strength against breakage.
The proportion of soot in polyethylene pipes at the time of production should be uniform, this will prevent weakening of the tensile strength of the pipe in places where soot accumulates to a high degree.
Polyethylene pipes at the time of production must have the same thickness and the pipe must be round and round without any priority. Polyethylene pipes are produced in 6, 9 and 12 meter strands and 125 sizes in rolls of 100 meters.
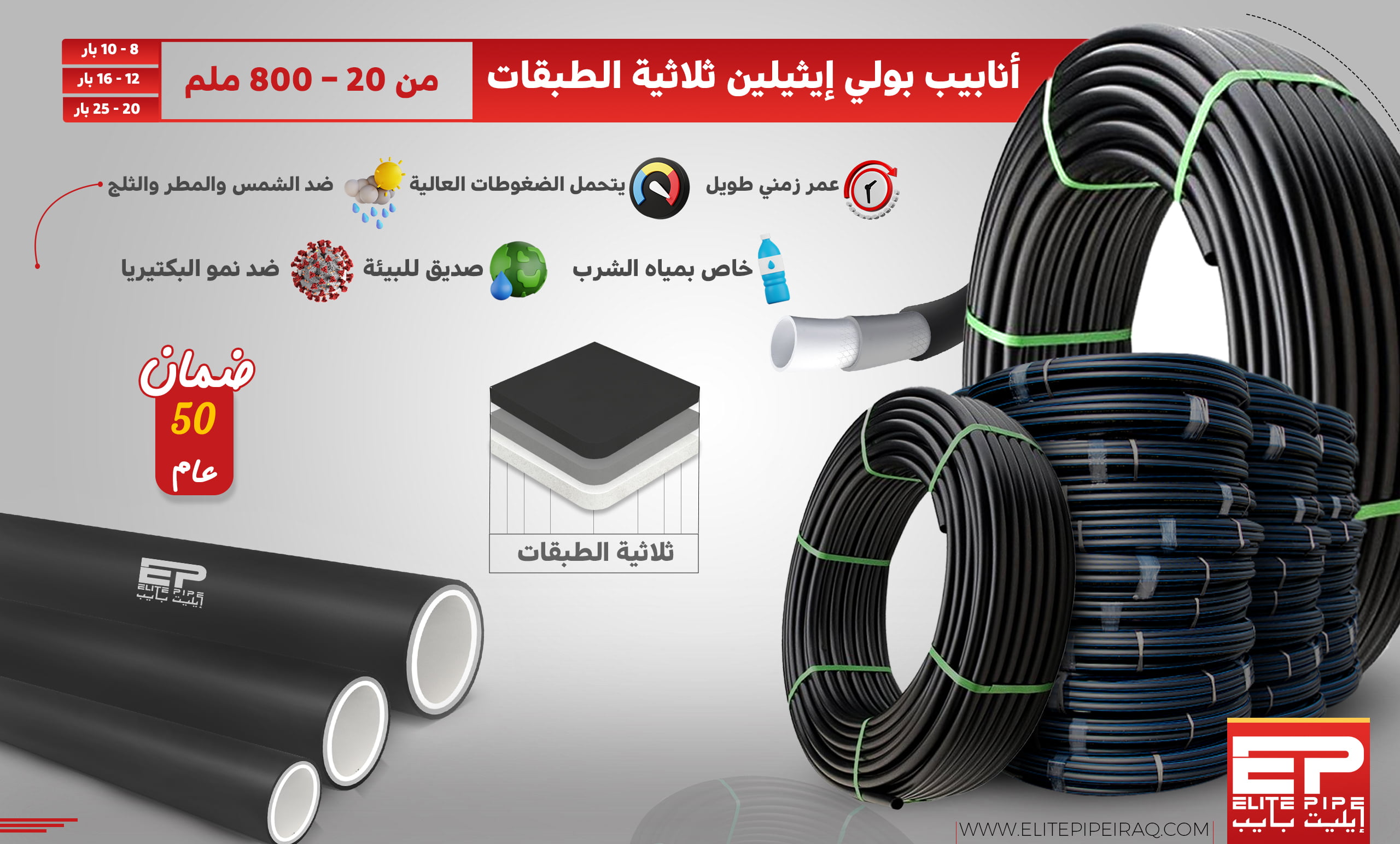
The cause of soot in polyethylene pipes
Ultraviolet light is one of the gaseous environments for polyethylene. Exposure of plastic products, for example polyethylene pipes, for long hours in the face of ultraviolet radiation, especially in the presence of oxygen and ozone, leads to chemical degradation under various mechanisms in their structure, and ultimately by weakening of the mechanical properties. The service life will be reduced.
Polyethylene pipes do not withstand ultraviolet rays from the sun and light sources that have the same shape on their own, and harmful ultraviolet rays cause their destruction. UV resistance can be increased by the presence of pigments in the desired polyethylene. Pigments can absorb radiation and prevent it from penetrating the mass of matter. Among black, white, blue and green pigments, soot is the best choice for increasing resistance to ultraviolet light.
Therefore, to prevent the penetration of these radiations, they create a soot-resistant light curtain as the cheapest anti-UV in these products.
For best performance of this curtain, at least 2% of soot should be evenly distributed in the tube.
A lower percentage of this amount of soot (2%) results in poor optimal performance of light-resistant curtains and higher than 3% causes poor other physical and mechanical properties of this product.
This amount of mixing, because it is done by the physical method, in most cases does not give a homogeneous mixture, and in some parts the amount of soot is less or more than the permissible limit, so the best way to achieve maximum quality is to use the materials: black primer (i.e. the granules used which Contains anti-UV to prevent molecular damage caused by the effects of sunlight while uniforming conditions for all parts of the tube.
Reliability
This factor, mentioned in the Iranian National Standards and the German DIN, determines the degree of safety and guarantees longevity. In other words, a pipe with a reliability factor of 1.25 means that the actual pressure tolerance in that pipe is 25% higher than its nominal pressure.
But in fact, this coefficient includes special cases such as withstanding cross-section stresses above the nominal limit or invisible or intangible defects that occur during production, transportation, loading and storage.
The coefficients specified in the standard are 1.25 – 1.6 – 2, for general cases the coefficients are 1.25 and in cases where the sensitivity is high, such as main arteries or fire lines, the coefficients are 1.6 and 2.
It should be noted that the thickness and weight of pipes vary with different parameters and at the time of design, contract, production, quality control and installation depend on these parameters.
Test to determine the percentage of soot in a polymer
Soot is an important additive added to basic polyethylene to increase the resistance of pipes to atmospheric invaders, especially ultraviolet light. Soot is measured using an electric furnace and the pyrolysis method. The permissible percentage of carbon in polyethylene pipe is 0.25.2.2% by weight and it must be evenly distributed throughout the pipe.
In areas where carbon accumulation is higher than the permissible percentage, stress concentration will occur and the tube will become weak, and if the carbon content is lower than the permissible level, the strength of the tube against the sun's ultraviolet rays will decrease. In this method, the soot remaining from the pyrolysis (thermocouple) of the sample is measured in an oven at a temperature of 500 to 600 °C, in the presence of nitrogen gas. Then, at a temperature of 850°C, the remaining amount of carbon is burned under the influence of oxygen to determine the percentage of ash (additives) in the prototype.
This method is used to determine the amount of soot in polyethylene, polypropylene and polybutylene. This method is not recommended for plastics modified with acrylic monomers or other polar monomers because it may affect the test. This method cannot be used for compounds containing dyes or non-volatile fillers other than smoke.
Equipment production line for polyethylene pipes and fittings
Raw material for polyethylene pipe
Polyethylene or polyethylene is one of the simplest and cheapest polymers. Polyethylene is a waxy, inactive solid. This substance is obtained from the polymerization of ethylene and is abbreviated as PE. The ethylene molecule contains a double bond C=C. In the double bond polymerization process, both monomers are broken, and instead a simple bond is formed between the carbon atoms of the monomers, and the resulting product is a large molecule.
Today, the use of polyethylene (PE) materials in pressure water supply and gas supply systems has grown significantly. It is natural that this significant growth will continue if over time we see the use of new technologies in raw materials, manufacturing process and methods for connecting and installing these types of pipes in industry.
In order to achieve the above goal – with a raw material approach – we have witnessed the production of different types of polyethylene, the third generation of this growing process of PE100 material, which since 1990 in Europe as a suitable grade in the pipe industry.
Comparing the third generation polyethylene materials (PE100) with the second generation (PE80), the important point according to ISO definitions is the minimum expected strength at an operating temperature of 20 °C after 50 years of pipe installation. This minimum strength is expected to be 10 MPa for PE100 and 8 MPa for PE80.
Types of polyethylene pipes based on raw materials
Polyethylenes are a family of resins obtained by polymerization of ethylene gas (C2H4). Through the catalyst and polymerization method of this material, various properties such as density, melt flow index (MFI), crystallinity, degree of branching and crosslinking, molecular weight and molecular weight distribution can be controlled. Low molecular weight polymers are used as lubricants.
Sometimes, instead of hydrogen atoms in a molecule (polyethylene), a long chain of ethylene is attached to carbon atoms, called branched polyethylene or light-duty polyethylene (LDPE); Because its density has decreased due to the increase in its work volume. In this type of polyethylene, the ethylene molecules are attached to each other randomly, creating a highly irregular shape and form. Its density is between 0.910/925. It is produced under high pressure and temperature, and free radical polymerization of vinyl is often used. Of course, Ziegler Nata polymerization can also be used to prepare it.
When there are no branches in the molecule, it is called linear polyethylene or heavy duty polyethylene (HDPE). Linear polyethylene is stiffer than branched polyethylene, but branched polyethylene is easier and cheaper to make. The shape and appearance of this polymer is highly crystalline. Linear polyethylene is a natural product with a molecular weight between 200,000 and 500,000, which is polymerized under relatively low pressure and temperatures. Its density ranges between 0.941 and 0.965, and it is mostly prepared through a formed process called Ziegler-Nata polymerization.
There is also polyethylene whose density is between the densities of these two polymers, i.e. in the range from 0.926 to 0.940; It is called semi- or medium-heavy polyethylene. Polyethylene with a molecular weight between 3 and 6 million is called ultra-ultra molecular weight polyethylene or UHMWPE and is produced by metallocene-catalyzed polymerization. The material is more difficult to process, but its properties are excellent. When the polymer is completely crosslinked by radiation or the use of chemical additives, the polyethylene will no longer become thermoplastic. This material will be a true heat hardener with good tensile strength, electrical properties and good impact strength over a wide range of temperatures when baked during or after forming. It is used to make a very strong fiber to replace Kevlar (a type of polyamide) in bulletproof vests; Also, his large boards can be used instead of ice rinks. By copolymerizing monomethylene with a branched alkyl monomer, a copolymer with short hydrocarbon branches is obtained, which is called linear low-density polyethylene, or LLDPE, and is often used to make things like plastic films.
Polyethylene pipes are divided into three categories in terms of raw materials
Polyethylene pipes with PE 63
PE 63 materials have a lower density than newer materials and therefore have greater weight and thickness, which makes the cost of producing polyethylene pipes with PE 63 materials much higher than newer materials, so the use of these materials is not economically justified and is now obsolete.
Polyethylene pipes with PE 80
The use of PE 80 materials in the production of polyethylene pipes became popular after manufacturers realized that by increasing the density of the raw material, with a lower thickness and weight, a pipe with greater pressure tolerance and a cheaper price could be produced.
Polyethylene pipes with PE 100
PE 100 material is the latest kind of raw material for producing polyethylene pipes, which is considered a high-quality material. PE 100 polyethylene pipes have greater density, less weight and thickness and can also withstand more pressure.
Advantages of PE100 polyethylene pipes over other raw materials
- Better processability, higher output and lower production costs
- Better flexibility in wrapping, fixing and installing pipes
- Higher resistance to slow crack growth and higher product safety factor
- Higher resistance to rapid crack growth
- Higher hydrostatic resistance
- Basic tips
In the production of 4x polyethylene sewer pipes up to size 125 (5 inches), PE80-PE100 materials cannot be used at all and only PE63 materials should be used in their production. Because the thickness of the pipe is very low, the possibility of the pipe bursting and breaking is very high, but PE80-PE100 materials for the production of large-sized pipes, especially the working pressures of 10 bar and 16 bar.
For example, a 10 bar 3-inch polyethylene pipe made of PE63 has a thickness of 8.2 and weighs 2.12 per meter, while a 3-inch PE80 polyethylene pipe has a thickness of 5.6 and weighs 77.77, respectively. 1 For PE100 polyethylene pipe, the thickness is 6.7 and the weight is 1.46.
Polyethylene pipes cannot be joined due to lack of solvent and do not have this ability and in this respect they differ from plastic pipes and are connected by heat welding of pipes or welding of pipes with welded joint or gear connections.